Usage Guidelines for Ceramic Anilox Rollers
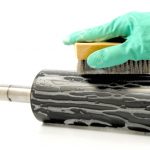
Usage Guidelines for Ceramic Anilox Rollers
-
Installation and Removal of Screen Rollers:
- Handle with care during installation, removal, and transportation. Gear bearings should be installed with thermal matching. Use specialized tools for removal to avoid forceful handling, as ceramic coatings are fragile.
- For larger rollers, consider using lifting equipment to prevent damage.
-
Initial Grinding of New Rollers:
- To prevent scoring on new rollers, use new ink and a new blade during the initial grinding period.
- Reduce blade pressure, ensure regular cleaning, and perform frequent inspections to maintain optimal performance.
- Avoid testing rollers without the initial grinding period to prevent color instability.
-
Shutdown and Idle Periods:
- During shutdown, prevent dry running of the roller. For short stops, keep the roller immersed in ink and rotating. For longer stops, clean promptly, detach the blade or rubber roller, and prevent uneven ink supply due to ink drying.
-
Storage and Inspection:
- Before storage, deep clean the roller, inspect the surface for damage, and use a 400x magnifying glass to check the condition of cells.
- Record usage and inspection results, store on a specialized stand, wrap the surface with clean, breathable paper, and avoid high-temperature, high-humidity storage spaces.
-
Establishment of Roller History Table:
- Implement a strict system to record roller usage, cleaning, storage, and any anomalies. This provides guidance for production and facilitates post-sale support applications.
- Low-quality inks and blades increase the risk of roller damage.
Ceramic Cleaning Methods
Given the characteristics of ceramic anilox rollers, any cleaning method should undergo safety testing. When purchasing cleaning equipment, demand a safety limit test report from the supplier. If unable to clean the roller effectively, seek assistance from the supplier.
-
Daily Manual Cleaning:
- Immediately clean with a solvent (water for water-based inks) after printing. Use a steel brush for scrubbing.
-
Specialized Cleaning Agent:
- Periodically, when visible dirt appears, use a specialized cleaning agent with a steel brush for a thorough cleaning. Neutral and alkaline cleaning agents are safer options.
- Several excellent cleaning agents on the market can effectively clean ceramic anilox rollers.
-
Ultrasonic Cleaning:
- Adhere to a low-frequency, extended soaking approach with a suitable cleaning agent. Based on experiments, limit each cleaning session to around 15 minutes for safety and increased roller lifespan.
-
Laser Cleaning:
- Laser cleaning is an efficient method for challenging cases. However, thorough safety testing is crucial before implementation.
-
Other Cleaning Methods:
- Other cleaning methods require thorough testing and safety reports from equipment suppliers before use.
Packaging and Storage
Inner packaging should be breathable and dry, such as parchment paper. Outer packaging should provide moisture and shock resistance. Avoid high-temperature, high-humidity storage environments. Store rollers in dedicated stands or wooden boxes.
1.Transfer Rate
Within a standard web opening/depth ratio of around 3:1, different patterns of anilox rollers show similar transfer rates. Use supplier-provided data on line count, depth, and ink volume to estimate actual ink quantity on the printed product.
2.Changes in Ink Volume
Regularly measure ink volume, especially as the roller ages and cell volume decreases. Specialized instruments or coating tests are effective methods for measurement.
Factors Affecting Cleaning Difficulty
Based on statistical research, factors influencing cleaning difficulty include:
- Coating Influence: Limited research on coating impact on cleaning difficulty.
- Web Wall Shape: Higher web wall proportions contribute to cleaning challenges.
- Ink Influence: The ink system, particularly water-based inks, affects cleaning difficulty. Adjustments in ink formulation may impact cleaning.
Impact of Cleaning Methods on Ceramic Anilox Rollers
-
Cleaning Agent Impact:
- Traditionally, acidic cleaning agents were considered to increase the probability of coating corrosion. While comprehensive data is lacking, industry observations suggest potential risks.
-
Ultrasonic Cleaning Impact:
- Ultrasonic cleaning can cause damage, including increased likelihood of scratching and higher probabilities of roller collapse. Extreme caution and adherence to recommended cleaning times are essential.
-
Laser Cleaning Impact:
- Laser cleaning results in microscopic damage to the roller. The safety and efficacy of laser cleaning should be thoroughly validated, including safety limit testing.
-
Powder Spraying, High-Pressure Water Cleaning, and Other Methods:
- Limited data is available on the impact of these methods on ceramic anilox rollers. Thorough testing and safety reports from equipment suppliers are essential before adopting these methods.
Types, Causes, and Responses to Anilox Roller Scratching
-
Particle Wear Type Scratching:
- Characterized by the appearance of scratches after some usage time. The width ranges from 2 to several cell widths. Address by reducing particles in the printing environment.
-
Web Wall Collapse Type Scratching:
- Typically occurs in the early stage, with narrow scratches, often only one web wall width. Indicates a quality issue in the roller and requires immediate contact with the supplier.
-
Particle Peeling Type Scratching:
- New rollers may show scratching after a few runs, particularly after ultrasonic cleaning. Contact with the supplier is necessary, as it indicates a quality issue.
Ceramic Anilox Roller Bubbling
Bubbling occurs when the base material corrodes, causing point-wise swelling. This leads to the ceramic layer rising and, in severe cases, detaching. Early-stage bubbling may result in uneven ink supply due to increased pressure on the affected point. Causes include coating quality, acidic environments, and prolonged use of ultrasonic cleaning.
Upon discovering bubbling, contact the supplier promptly to investigate the cause.